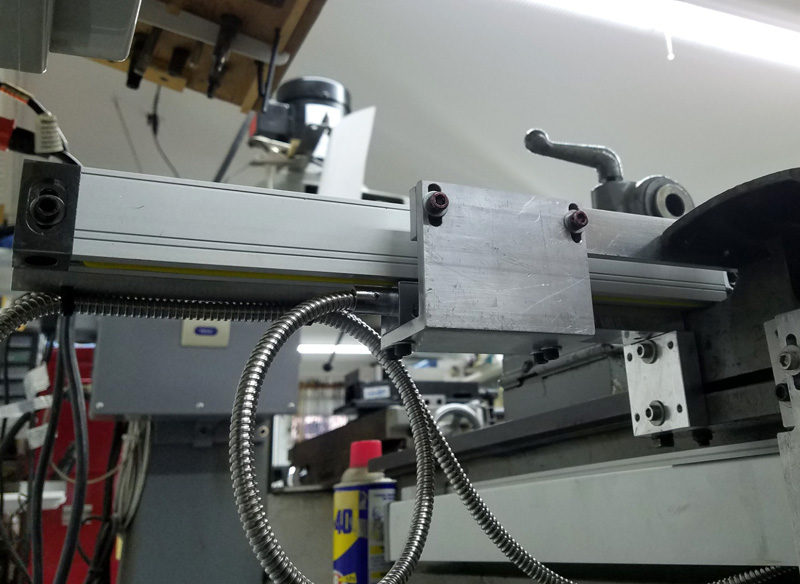
The left shows the X axis from the tailstock end of the lathe.
You can see the adjustable mounting block, and the somewhat narrower
support bar attached at right angles. To this bar is
fastened the 1/4 inch thick angle with the leg facing us.
The right shows it from the headstock end. We can see the scale
attached to the flat side of the angle and the trolley driving
brackets. I used the mounting rail which previously supported the
capacitive scale intact except for adding one threaded hole and it is now used to drive the trolley.
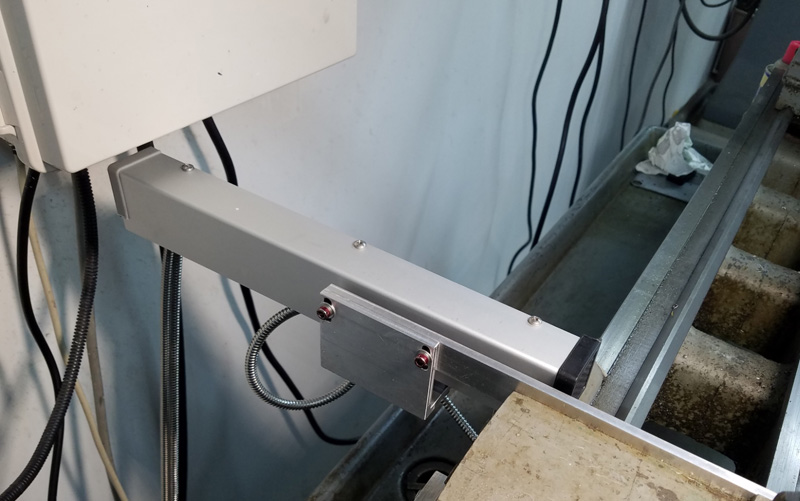
I left the design of mounting the X scale cover until after mounting
everything else, to see just what I needed to work around etc.
When fitting the cover I found I needed to raise it
3/16 to 1/4 inch and provide tapped mounting holes to attach the
cover. I had some 1/4 square aluminum bars with many tapped 4-40
holes. I drilled out 3 and tapped them to
8-32, then used JB Weld epoxy to attach the bars to the top of the
angle. This gave me both the space and the mounting holes.
To make sure the epoxy bond on the thin 1/4 inch wide angle
would withstand a force or a blow to the top (heaven forbid!), I
attached several stick-on soft plastic feet to the inside of the cover
side, to bear on the scale if the cover is pressed down.
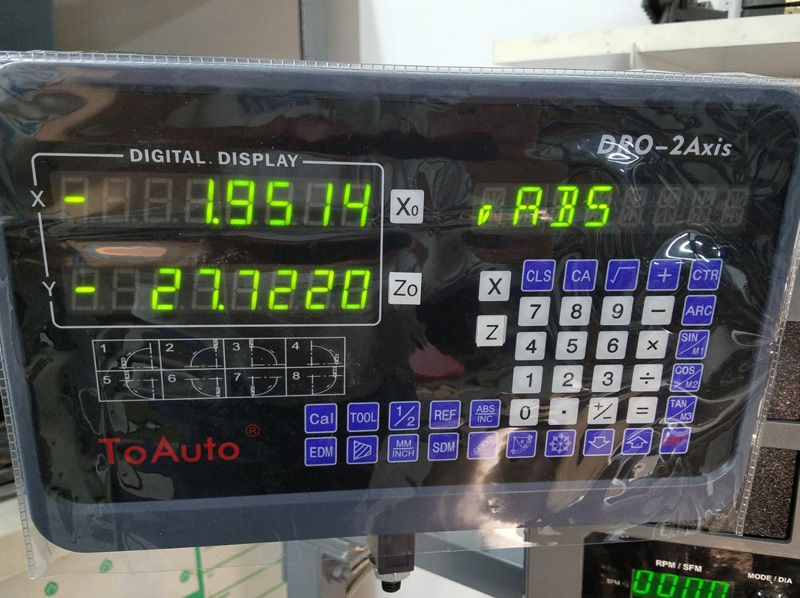
This is the DRO display. There are many special functions which would be applicable to a mill, such as bolt circles,
lines of holes at any angle, and rounded surfaces, which make no sense for a lathe. One feature which may be
very useful is a 200 entry tool library. This would allow changing from one tool to another without having
to re-calibrate the readings on the DRO. The differences in dimensions would be automatically adjusted
as you specify a different (pre calibrated) tool.
The small triangle before the "ABS" (absolute mode) indicates that the X cross slide axis is reading double the
actual movement. Knowing the part's diameter is usually more useful than the radius.
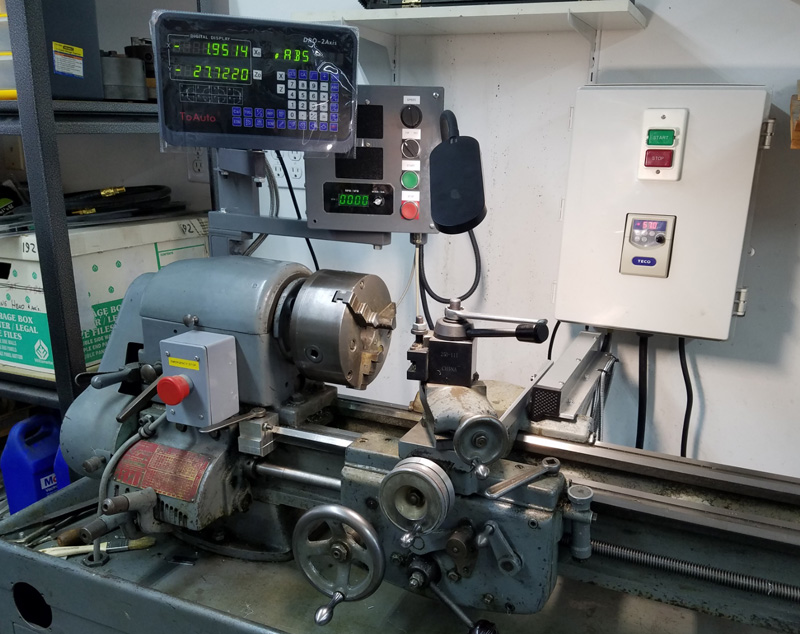
Here is the finished installation. The DRO powers up whenever the
power is turned on to the lathe. The readings are remembered
from one cycle to the next, as long as the carriage and cross slide
have not been moved while the power is off. The display is mounted
using the included hardware. I mounted it to a small piece of oak
which is attached to the crossbar holding the control box. I
raised the
mounting of the lathe's power box on the wall to allow the extended X scale to pass under it.